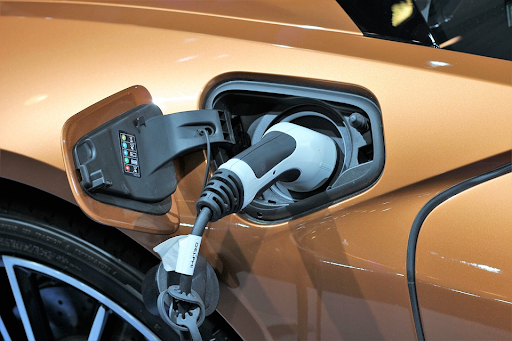
The good news for the automotive industry is that the ongoing semiconductor shortage won’t last forever. Some experts are pinning the eventual recovery phase at 2023. However, a lithium battery shortage could immediately follow in its wake. Forbes reports that battery scarcity could dwarf the impact of the chip shortage on the automotive supply chain — but not until the second half of the 2020s.
A Tale of Two 2020s for the Automotive Industry
The coming global pivot to electric vehicles (EVs) will be a primary catalyst in the looming battery shortage, but auto manufacturers will face unique challenges in each half of the 2020s.
As automakers ramp up development and production of EVs, the advanced lithium ion batteries that they rely upon will experience an enormous surge in demand. Research from CAR suggests that while the semiconductor shortage will ultimately reduce global production of cars by 8.1 million between 2021 and 2023, the supply chain is likely to lose another 18.7 million (electric) vehicles between 2022 and 2029 due to a shortage of EV battery cells.
“The global car market is characterized by two bottleneck factors up to the year 2030,” said Professor director Ferdinand Dudenhoeffer of CAR. “On the one hand, there is a shortage of semiconductors which will have an impact until the beginning of 2023, and then an important battery cell availability problem.”
Yang Hongxin, chairman of SVolt Energy Technology Co., agrees. “When the chip shortage is over, the major supply shortage the industry faces would be batteries,” he told Bloomberg. Hongxin foresees tight production capacity for battery cells until much later in the decade “because expansion takes time.”
Not Materials, But Capacity
Availability of battery components like copper foil and cathode materials may represent short-term issues due to disrupted supply chains. However, materials are not likely to be the culprit in a lithium battery shortage that could last until 2030.
The high current price of lithium has done little to spark interest in necessary capacity-increasing investments. Long-term contracts at current levels have simply offered more attractive prices. This will cause trouble as demand soars, because the infrastructure required to meet production demand will take time to build out. “Unless we see significant and imminent investment,” George Miller of Benchmark Mineral Intelligence (BMI) told Reuters, “these shortages will extend out to the end of the decade.”
As chief executive Kim Jun of SK Innovation observed in a piece on Ford’s EV efforts, “The current U.S. battery capacity is far short of meeting demand. Building a factory to meet demand requires a lead time of 30 months,” a timeframe that would include factory site selection, construction and product testing. “Cell manufacturing is not that simple. It has to go through a lot of trial and error.”
Verified Quality Matters Most
In recent panel remarks published on Utility Dive, principal BMI consultant Vivas Kumar explained that quality was the crux of the issue. “What matters is the production of a high-purity, high-quality chemical that can be used in battery manufacturing,” Kumar said.
Kumar is a former senior manager for Tesla’s battery supply chain and foresees clear obstacles ahead. Rather than a shortage of raw materials, supply problems are likely to result from a shortage in “the number of companies that can produce a large volume of these high-purity chemicals,” which is both “very small” and “constantly capital-constrained.”
The research process for delivering new technologies is long and involved. Jacqui Murray, deputy director of a UK fund for developing new EV battery tech, called the battery development process “quite bespoke, very complex.” Fellow panelist Doug Campbell, chief executive officer at Solid Power, reinforced the point. “Any time you’re developing a new battery chemistry, that is hard, hard work. I don’t want to trivialize how much effort goes into developing a chemistry to meet requirements,” he said.
Accelerate EV Battery Testing With Energy Assurance
The complexity of testing, urgency of demand, and influx of new battery factories will put extreme pressure on the EV supply chain. Internal testing labs at automaker facilities are unlikely to be able to keep up on their own.
Strategic investment in a third-party testing lab partnership can accelerate results without sacrificing rigor or compliance. From battery performance testing to failure analysis, engineering analysis, and safety testing, a properly equipped battery testing partner can offer a combination of experience and capabilities to ensure reliability as the supply chain evolves.
Energy Assurance is the largest cell and battery testing lab in North America. When you work with our experienced team, you’ll realize a dramatic increase in EV battery testing capacity and speed with great confidence in the results. Get in touch with Energy Assurance today to share the details of your next project and learn more about how we can help.